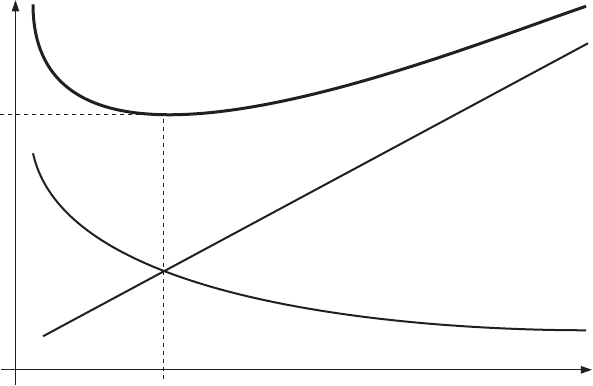
270 CHAPTER 11 MANAGING RISKS
What you need, when you need it
Too much inventory costs you money. It ties up cash in stock that can, of course, become
obsolete or damaged. At the other extreme, not enough inventory tests customer loyalty
and leads to lost or delayed sales. Remember how you reacted last time that you were
told that something you wanted was out of stock?
You know your minimum inventory levels (established in Chapter 8). Obviously this is
not necessarily the optimum level, but it can be identified using some simple arithmetic.
Consider that the only things that vary are:
Ordering costs – the costs of processing purchase orders, taking delivery and/
or tooling up for a production run, and so on. Ordering costs per unit decline as
volumes increase due to economies of scale.
Carrying costs – including premises, insurance and funding costs. These increase
steadily with volume.
Figure 11.6 shows these costs separately and combined. The optimum inventory level is
where ordering and carrying costs are minimised, which is where they equal each other.
In other words, in any one period, the quantity of inventory that you should order is the
quantity where:
total ordering costs = total carrying cost
or
number of orders × cost per day = average inventory × carry cost per unit
Minimum
inventory
cost
Money
Units of inventoryOptimum
inventory level
Total inventory
cost
Inventory
carry cost
Inventory order cost
Figure 11.6 Optimum inventory level